Understanding Prototype Injection Molds: A Comprehensive Guide
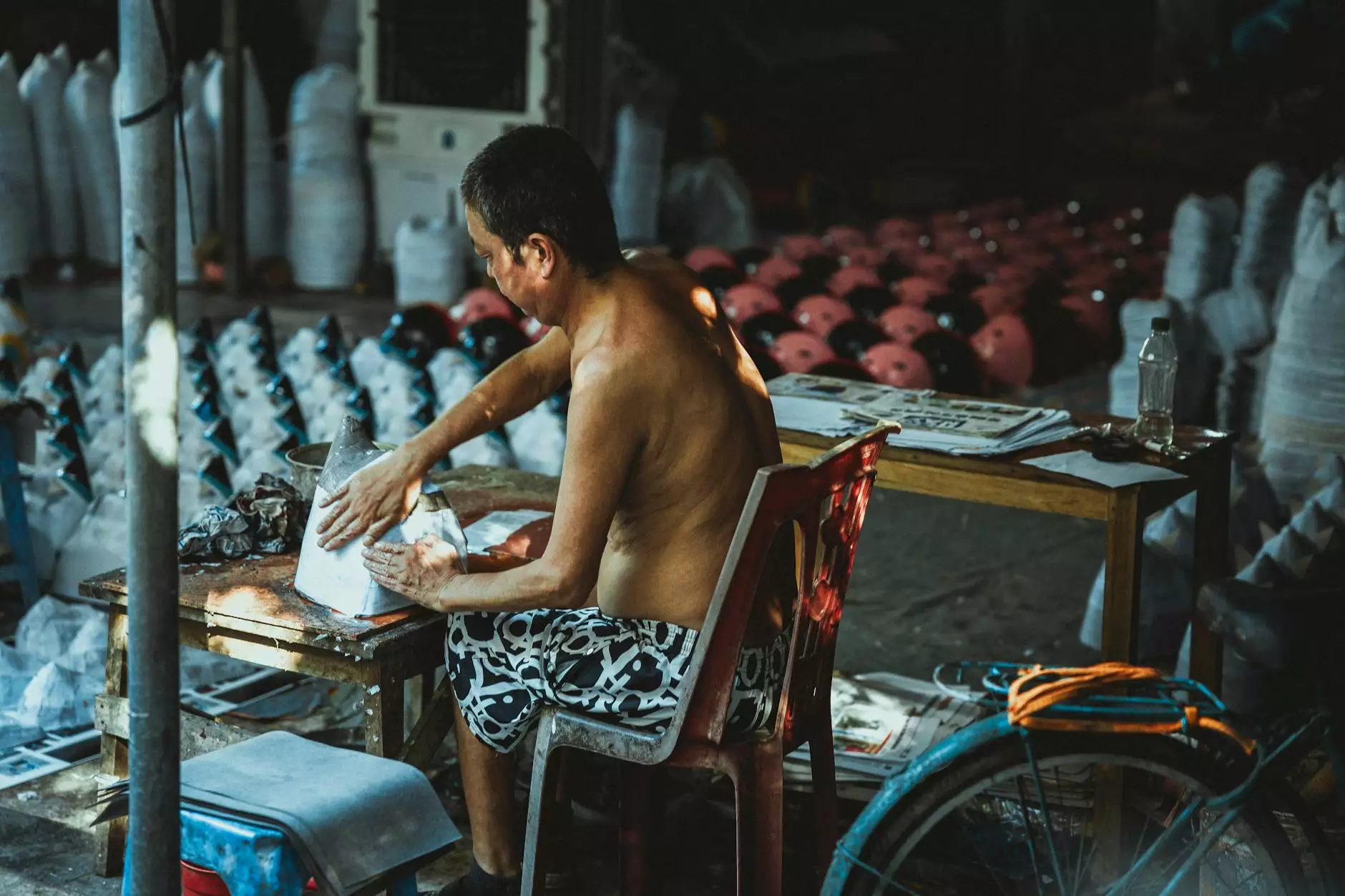
The world of manufacturing is constantly evolving, and one of the crucial aspects that underpin this evolution is prototype injection molds. These molds serve not only as a foundation for product development but also as a bridge connecting innovative concepts to tangible goods. As businesses seek to improve efficiency, reduce costs, and enhance product quality, understanding the role of prototype injection molds has never been more essential.
What are Prototype Injection Molds?
Prototype injection molds are specifically designed tools used in the initial stages of the product development process. They allow manufacturers to create prototypes that closely mirror the final product's design and functionality. This process is critical for assessing design integrity, functionality, and manufacturability before mass production begins.
The Importance of Prototype Injection Molds in Product Development
In the realm of manufacturing, the importance of developing a robust prototype cannot be overstated. Below are several reasons why prototype injection molds play a pivotal role:
- Testing and Validation: Prototypes allow for extensive testing, which is essential for validating design concepts and identifying potential flaws before they escalate into costly mistakes during mass production.
- Speed to Market: By utilizing prototype injection molds, businesses can dramatically shorten the time from concept to market. Rapid prototyping enables quick iterations and adjustments based on feedback.
- Cost Efficiency: Creating prototypes using injection molds helps in identifying production costs early in the process. This leads to more informed decision-making and budget allocations for final production.
- Enhanced Communication: Prototypes serve as a tangible representation of ideas, allowing design teams and stakeholders to communicate more effectively, ensuring everyone is aligned on the product goals.
The Process of Creating Prototype Injection Molds
The creation of prototype injection molds involves several critical steps that ensure the final product meets design and functional specifications. Here’s a breakdown of the process:
1. Design Development
Every successful project begins with a comprehensive design plan. Advanced computer-aided design (CAD) software is used to create a digital representation of the product. This design must be meticulously crafted, considering factors such as material properties, part geometry, and assembly processes.
2. Material Selection
The selection of the right material for the mold is crucial. Different materials, such as steel, aluminum, or even hybrid composites, can influence the mold's durability, heat tolerance, and ease of machining. Selecting an appropriate material can significantly affect the quality and longevity of the prototype.
3. Mold Fabrication
Once the design is finalized and materials chosen, the actual mold fabrication begins. This step involves CNC machining, electrical discharge machining (EDM), or 3D printing techniques to create the mold based on the specifications outlined in the design phase. Precision is paramount to ensure that the mold will produce accurate prototypes.
4. Injection Molding Process
After the mold is created, the next step involves injecting the selected thermoplastic materials into the mold. This process usually takes place under controlled temperatures and pressures to achieve the best results. The injected material is allowed to cool and solidify into the desired shape.
5. Prototype Evaluation
Once the prototypes are produced, they undergo rigorous testing and evaluation. Engineers and designers assess several factors, including dimensional accuracy, surface finish, and overall functionality. This stage is critical for identifying any necessary design modifications before final production.
Advantages of Using Prototype Injection Molds
Leaning toward prototype injection molds comes with various advantages that fuel innovation and efficiency in manufacturing practices. Here are a few of the key benefits:
- Precision and Repeatability: Injection molding provides high precision in part manufacturing, ensuring consistent quality across multiple prototypes. This repeatability is vital when scaling to mass production.
- Complex Geometries: Prototype injection molds can accommodate complex shapes and structures that may be challenging or impossible to produce with other methods. This flexibility allows businesses to innovate without constraints.
- Material Variety: The injection molding process allows for the use of a wide range of materials, giving product designers the freedom to choose materials that best suit their functional and aesthetic requirements.
- Reducing Waste: Since injection molding is a highly efficient process, it typically results in less waste compared to traditional machining methods. This environmental benefit is becoming increasingly important in contemporary manufacturing.
Applications of Prototype Injection Molds
The applications of prototype injection molds span across various industries — each benefiting from precision, efficiency, and the ability to innovate rapidly. Here are some notable sectors:
Aerospace Industry
In the aerospace sector, where safety and performance are critical, prototype injection molds are essential for creating lightweight yet robust components. The ability to iterate designs quickly helps aerospace manufacturers enhance efficiency and performance metrics.
Automotive Industry
The automotive industry frequently utilizes prototype molds to test new designs for everything from dashboards to engine components. Rapid prototyping ensures that parts are tested under real-world conditions, leading to safer and more reliable vehicles.
Consumer Electronics
With technology advancing at breakneck speeds, the consumer electronics sector relies on prototype injection molds to keep up with the demands for innovative and sleek designs. Prototyping plays a critical role in product launches, helping firms stay competitive.
Medical Devices
In the medical device field, precision can be a matter of life and death. Prototype molds allow for quick adjustments and validations of design specifications, ensuring that products meet strict regulatory standards before entering the market.
Conclusion
In conclusion, prototype injection molds form an integral part of the product development lifecycle in various industries. They foster innovation, enhance communication, and ultimately improve the quality and efficiency of manufacturing processes. As a leader in the metal fabrication industry, deepmould.net understands the importance of using high-quality prototype molds in driving business success. Embracing these advanced practices will position your business not only to stay competitive but also to thrive in today’s dynamic marketplace.
Investing in prototype injection molds is not merely a choice but a necessity for businesses aiming for precision and innovation in their product offerings. As you delve deeper into your manufacturing processes, keep the importance of prototyping at the forefront, ensuring that every new product launched is not only innovative but also market-ready from day one.